Innovations in the 17th-century glass industry:
the introduction of kelp (seaweed) ash in Britain
David Dungworth
English Heritage, Fort Cumberland, Portsmouth (United Kingdom).
The 17th century saw many innovations in the British glass industry. The adoption of coal fuel and the development of a stable colourless lead-based glass are well known. This paper examines a less well known innovation: the use of seaweed (kelp) ash as an ingredient in glass manufacture. While there are a few historical sources which mention the use of kelp, recent chemical analysis of historic glass has provided new insights. Chemical and isotopic analyses allow the identification of a class of 17th- and 18th-century glass which was made using kelp. This glass is a mixed alkali glass (it contains significant proportions of both sodium and potassium) which has a strontium content that is far higher than other contemporary glasses made using the ashes of terrestrial plants. Seaweed is known to contain high concentrations of strontium. This identification is further strengthened by a comparison of the strontium isotope ratios in this glass and modern seaweed.
Innovations dans l'industrie verrière anglaise au XVIIe siècle :
l'introduction du varech dans la composition.
Le XVIIe siècle voit beaucoup d'innovations dans l'industrie verrière anglaise. L'introduction du chauffage au charbon et le développement du verre au plomb (cristal) sont bien connus. Cette contribution porte sur une innovation moins connue : l'utilisation de cendres d'algues (varech) comme ingrédient dans la composition.
Peu de sources historiques mentionnent cette innovation, mais de récentes analyses chimiques ont apporté des éléments neufs. Les analyses chimiques isotopiques ont permis d'identifier une série de verres datés du XVIIe et XVIIIe siècles fabriqués avec du varech. Le verre, de composition alcaline mixte (il contient en proportion significative de la soude et de la potasse) possède aussi du strontium dans une proportion largement plus haute que celle d'autres témoins fabriqués à partir de cendres de végétaux terrestres. Or on sait que l'algue contient de grandes concentrations de strontium. Cette identification est confortée par la comparaison des ratios isotopiques de strontium dans la composition de ces verres anciens, et dans des algues contemporaines analysées à cette fin.
Introduction
The 17th century saw a number of significant technological developments in the British glass industry. The ban on the use of wood as a fuel in the second decade of the 17th century led to the relocation of most glasshouses from rural, woodland areas to the Coalfields. By the middle of the century, the British glass industry had begun to produce the so-called 'English bottle', that is those thick-walled, dark green bottles that were used for the storage of wine and other drinks. The last quarter of the 17th century saw the development of a colourless lead-based glass used for the manufacture of fine tablewares. Less well known is the adoption of the ashes of seaweed (kelp) in the glass industry. Kelp ash was introduced into the glass industry around the middle of the century and continued in use, especially in the crown window-glass industry, until the 1830s. After providing a summary of the historical evidence for the use of kelp ash in the British glass industry, this paper presents scientific data which allows the use of kelp to be recognised in particular artefacts.
Historical evidence for the use of kelp ash in glass manufacture
There is substantial historical evidence for the use of kelp ash in glass manufacture from the 1660s until the 1830s. Christopher Merrett's 1662 English translation of Neri's The Art of Glass (Cable 2001) contains a substantial commentary on the modes of glassmaking in England at that time which includes the following:
The common sea-wrack […] is thrown and scattered upon the rocks, in great abundance, and also on the shoar, which country people in the summer rake together, dry it as they do hay, by exposing it to the sun and wind, and so turning it as occasion serves till 'tis fit to burn, and make these ashes call'd kelp, used as well to make alume as glass.
Cable (2001, 322)
The Oxford English Dictionary suggests that the term kelp is of rather ancient origin, however, it does record the earliest use of kelp ash as 1663. Eduard Lhuyd's Parochialia (originally published c. 1698) reports that seaweed was collected along the shore in the Vale of Glamorgan and burnt to form kelp that was shipped to Bristol for the glass industry (Lhuyd 1909). The use in this way of what was in many ways marginal land quickly spread to Ireland (Forsythe 2006) and Scotland (Gray 1951).
For much of the 18th century the use of kelp in glass manufacture, or in any other industry, was rarely remarked. Nevertheless, its continued use is indicated by some of the newspaper notices which advertised the sale of glasshouses. A Bristol glasshouse was advertised for sale in 1766 as comprising:
The stock, implements, utensils, kelp, fret, sand, ashes, pots, bricks, clay and a great many other things commonly used in making crown window glass.
(Buckley 2003, 91-2).
In his Chemical Essays, Dr Richard Watson describes the collection and burning of seaweed for the production of kelp or kelp ashes (Watson 1782, 119). He makes it clear that kelp contained a lower proportion of alkalis than barilla and that the latter material was preferable (although this ignores the fact that barilla was considerably more expensive). Samuel Parkes describes the use of 2 parts kelp and 1 part sand in the manufacture of crown window-glass (Parkes 1823, 192). Parkes also reveals that kelp only contained between 1 and 8% soda (Parkes 1823, 586).
While the Leblanc process for the manufacture of sodium carbonate from common salt was developed in France at the end of the 18th century, it was not introduced into Britain until the 1820s (Clow and Clow 1952, 110-112). Writing in 1860, Sheridan Muspratt describes how:
Not more than thirty years have elapsed since crown and sheet glass were manufactured from the crude alkali obtained from kelp […]. The kelp was used simply in combination with sand — the kelp containing soda and potassia, and furnishing the necessary amount of lime; but the glass thus produced was of very variable, and often inferior quality.
Muspratt (1860, 200-202)
Clearly some glass manufacturers did not immediately change from kelp to soda ash. Cooper reported that crown window-glass was made using kelp and sand (Cooper 1835, 23-26) but that the use of kelp was at that time declining in favour of sodium carbonate (Cooper 1835, 115). By the 1840s, however, Ure reported that crown glass could be made from kelp and sand but, 'instead of kelp, soda ash is now employed' (Ure 1844, 586). Indeed Gray reports that the kelp industry was already in decline in 1830 and had virtually disappeared by 1840 (Gray 1951, 205).
Archaeological evidence for the use of kelp ash in glass
The scientific analysis of samples of glass provides evidence for the introduction of kelp in the 1660s and its use until the early 19th century. The most convincing indicator of the use of kelp is the presence of significant concentrations of strontium oxide (SrO) in the glass. The use of seaweed is further confirmed by strontium isotope analysis.
The chemical composition of most post-medieval glass shows that it was manufactured using sand and the ashes of plants (Table 1). The potassium-rich forest glass produced throughout much of northern Europe during the medieval period is believed to have been made using the ashes of bracken (verre fougère). The high-lime low-alkali (HLLA) glass developed in Germany and France in the late medieval period was probably made using the ashes of trees (especially oak). During this period the sodium-rich glass produced in southern Europe (in particular in Venice) was made using the ashes of halophytic plants such as Salicornia (these ashes were traded under the name barilla). The 17th century saw the appearance of glass which contained significant proportions of both sodium and potassium. While mixed alkali glasses could be made using a variety of plant ashes, there is scientific evidence that some was made using seaweed.
The analysis of glass production waste from the earliest phase of glass working at the glasshouse at Silkstone, South Yorkshire (probably 1655-1670), showed the production of a mixed alkali glass with a significant concentration of strontium oxide (Dungworth and Cromwell 2006). While forest and HLLA glasses usually have strontium oxide concentrations of up to 0.1wt%, the earliest Silkstone mixed alkali glass contains 0.27wt%. Analysis of glass-working waste from 18th-century crown window-glass production sites in Bristol has shown strontium oxide concentrations up to 0.5wt% (Dungworth 2007; Jackson 2005). Examples of crown window-glass installed at Shaw House, Newbury in the first quarter of the 18th century, contain similarly high concentrations of strontium (Dungworth and Loaring 2009). The strontium to calcium ratio in this mixed alkali glass is much higher than is normally found in terrestrial plant ashes and limestones, but is comparable to that seen in seaweed (Li 2000).
Site | Idehurst South1 | Idehurst North1 | Tanland1 | Silkstone2 (Phase 1) | Silkstone2 (Phase 1) | Silkstone2 (Phase 2) | Bristol3 | Bristol3 |
---|---|---|---|---|---|---|---|---|
Type | Forest | Forest | HLLA | HLLA | Mixed Alkali | Mixed Alkali | Mixed Alkali | HLLA |
Date | c.1530-c.1550 | c.1550-c.1590 | c.1567-c.1615 | c.1655-c.1670 | c.1655-c.1670 | c.1670-c.1680 | c.1710-c.1770 | c.1710-c.1770 |
Na2O | 3.0±0.3 | 2.1±0.2 | 1.5±0.5 | 1.5±1.1 | 8.3±0.4 | 6.9±0.4 | 7.4±0.7 | 2.2±0.4 |
MgO | 8.7±0.2 | 7.2±0.2 | 2.8±0.2 | 5.4±0.7 | 5.5±0.3 | 2.9±0.1 | 5.0±0.3 | 4.7±0.2 |
Al2O3 | 1.4±0.2 | 1.1±0.1 | 2.2±0.2 | 4.0±0.5 | 3.1±0.1 | 1.4±0.3 | 3.4±0.3 | 5.4±0.3 |
SiO2 | 53.3±0.8 | 55.3±1.8 | 61.2±1.1 | 54.1±3.0 | 62.7±0.2 | 68.2±2.1 | 67.4±1.3 | 56.7±1.0 |
P2O5 | 3.9±0.1 | 3.2±0.5 | 2.2±0.2 | 3.2±1.0 | 1.3±0.1 | 0.3±0.4 | 0.9±0.1 | 0.9±0.2 |
K2O | 10.8±0.8 | 11.6±0.6 | 3.8±0.8 | 8.0±1.6 | 5.9±0.1 | 6.7±0.1 | 4.5±0.4 | 2.6±0.2 |
CaO | 16.6±0.5 | 17.0±0.3 | 24.2±0.9 | 20.5±2.2 | 9.3±0.2 | 10.6±0.1 | 10.4±1.1 | 23.9±0.1 |
MnO | 1.0±0.1 | 1.1±0.1 | 0.7±0.1 | 0.8±0.5 | 0.4±0.0 | 1.0±0.1 | 0.1±0.0 | 0.3±0.1 |
Fe2O3 | 0.6±0.1 | 0.6±0.1 | 1.3±0.1 | 2.1±0.3 | 1.1±0.0 | 1.1±0.2 | 0.7±0.1 | 2.5±0.1 |
SrO | 0.07±0.01 | 0.07±0.01 | 0.10±0.01 | 0.06±0.02 | 0.27±0.01 | 0.05±0.01 | 0.41±0.03 | 0.12±0.02 |
Table 1. Chemical composition of a range of medieval and post-medieval glasses (average values and standard deviations) [Sources: 1 = Dungworth and Clark 2004; 2 = Dungworth and Cromwell 2006; 3 = Dungworth 2007].
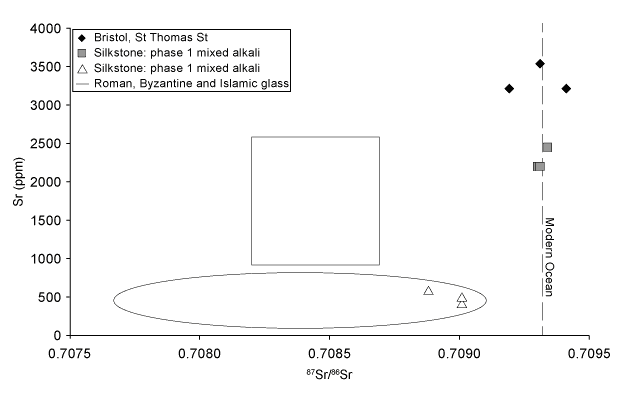
Figure 1. Strontium oxide content and strontium isotope ratio (Sr87/Sr86).
The relatively high strontium concentration of much of the mixed alkali glass produced in Britain from the late 17th century to the early 19th century indicates that this glass was made using kelp ash. In order to provide further scientific evidence for the use of kelp ash, samples of this mixed alkali were analysed to determine the ratio of strontium isotopes. The strontium isotope ratio of plants and their ashes are usually closely related to the geological context in which the plants grew. The strontium isotope ratios of rocks vary depending on a variety of factors but almost none have the same isotopic ratio as modern seawater. The strontium isotope ratios of high-strontium mixed alkali glass from Silkstone and St Thomas Street was close to that of modern seawater showing that the kelp was the most likely source of the strontium (Figure 1). Although a number of sites provide evidence for the manufacture of mixed alkali glass using seaweed, some sites show the production of mixed alkali glasses with low strontium content. The phase 2, low-strontium mixed alkali glass from Silkstone, had a strontium isotope ratio consistent with a terrestrial plant ash. A similar low-strontium mixed alkali glass was also produced in the late 17th century at Vauxhall, London (Dungworth 2006).
The origins of the use of kelp ash in glass
At the present time the origins of the use of kelp ash in the manufacture of glass remain obscure. From the end of the 17th century the use of kelp ash in the glass industry was most strongly associated with the manufacture of window glass and crown window glass in particular. While crown window glass was produced in England in the 16th century (Godfrey 1975, 22) it seems likely that it was largely abandoned in favour of broad or cylinder glass for most of the 17th century. Towards the end of the 17th century crown window glass production appears to have been re-introduced into Britain. John Bowles was involved in several glasshouses in South London and by 1691 claimed to produce crown window glass (Buckley 2003, 185). Bowles declared that he had 'sent one of his workmen to France to acquire information secretly either by bribery and corruption or some sort of espionage' (McGrath and Frost 1937, 22). It is possible that Bowles sent his workman to Normandy, which had a long tradition of crown window glass manufacture and which may have made use of seaweed (or varec) ash as a source of alkali (Chapman 1970). A Norman origin for the use of kelp ash in glassmaking might be valid. However, the archaeological and historical evidence reviewed in this paper shows that it was used in the 1660s, at least 20 years before Bowles claimed to produce crown window glass. No samples of mixed alkali glass with a relatively high strontium content have yet been identified earlier than those produced at Silkstone in the 1660s. It is curious that the earliest glass-working site in Britain with evidence for the use of kelp ash is 100 km from the sea.
Conclusions
The post-medieval glass industry was marked by a number of technical innovations which revolutionised the types of glass manufactured and their cost. The effect of these innovations was to transform glass from a material used only by the most wealthy sections of society to one available to all. The nature of these innovations varied from the dramatic ruptures with past practice, such as the development in England in the last quarter of the 17th century of a colourless lead-based glass (Dungworth and Brain 2009). In contrast, the adoption of seaweed ash as a flux in the English glass industry (and in particular in the window glass industry) is a more subtle innovation. In northern Europe various forest plants were used for the production of ashes used in glassmaking, while Mediterranean glassmakers tended to use halophytic plants growing in coastal regions. The use of seaweed as a source of alkali may have originated as a result of northern European glassmakers looking for suitable coastal plants.
David Dungworth