1. Broad glass manufacture in the English forests
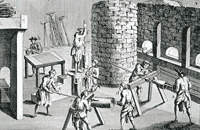
Fig. 1: Making broad/cylinder glass in the 18th century (Diderot).
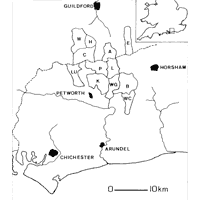
Fig. 2: Map of the Weald of south-east England (after Crossley 1994, 65).
Broad glass (sometimes referred to as Cylinder or Muff glass) was made by blowing a bubble of glass, elongated by swinging, cutting the cylinder lengthwise, and flattening on a smooth surface (marver) (Figs 1 and 15). This contrasts with Crown glass, for which a bubble of glass was spun to form a disc, or Cast Plate glass, which was poured on to a flat surface.
There is evidence for the manufacture of broad glass in England in the period 1570-1620. Much of our information comes from the Weald of Sussex and Surrey (Fig. 2), whence broad glass was exported. Prior to this, the evidence is less clear, and the existence of broad glass manufacture depends on the interpretation of the term ‘brodeglass’. and whether in the middle ages this was used for any form of flat glass. For example, John Glasewryth was recorded as making ‘brodeglas’ in 1380, but no details are known of his products.
The 16th-century evidence from the Weald links immigrant French glass makers with broad glass production. In 1569 Peter and John Bongard are referred to as glassmakers ‘… making of brode glasse’. In 1616 Isaak Bungard and Edward Henzey were described as ‘broade glass makers’, and again Izaak Bungard in the following year. Late-16th-century customs records for the west Sussex ports refer to the export of ‘broade burgundy glass’, which, given the tradition of making broad glass in eastern France, leaves little doubt that broad rather than crown glass was being described.
There are numerous glass-furnace sites in the Weald whose locations are known, and although only two have been excavated, neither of them used after c.1550, surface scatters of glass have been collected from several others. Those deposited in the museums at Guildford and Haslemere, Surrey, include recognisable fragments of broad glass, with its characteristic straight edges. Also, bubbles in broad glass are often in straight lines, compared with the concentric curves of the imperfections in crown glass. Broad glass is apt to be flatter than crown, the latter thickening towards the central pontil mark. A broken fragment of Purbeck marble, found at the furnace site in Idehurst Copse, Sussex is thought to be the remains of a marvering slab, on which cylinder glass was flattened.
In general, glass became cheaper in real terms during the period 1570 to 1615, as the efficiency of wood-fired furnaces increased and the market developed. Within this pattern, broad glass was cheaper than crown glass, and was therefore more commonly used in the smaller houses of the less well off. For example, in 1576 crown glass cost 3.2 pence per square foot, whereas broad glass cost 2.1 pence. Broad glass benefited from having a larger proportion of usable glass in each sheet, compared with what could be used from a crown-glass disc. However, crown glass often had a finer finish, and at least part of the disc could be thinner than the average broad-glass sheet.
∧ Back to top2. Post-medieval growth in the market for window glass
Throughout the 16th, 17th and 18th centuries, the English market for window glass was strong. The demand was due in part to the construction of large country houses, many built after ex-monastic land was sold by the Crown to lay landowners after the dissolution of religious establishments (c. 1535-40). The architectural styles adopted by craftsmen-architects such as Robert Smythson owed much to royal palaces such as Nonsuch, Surrey (Fig. 3) which were in turn inspired by continental designs embodying large glazed areas. The large windows of late-16th-century houses such as Smythson’s Hardwick Hall, Derbyshire (Fig. 4) contrasted with those of late-medieval houses, such as Kirby Muxloe, Leicestershire (Fig. 5) whose windows had usually been small, partly because of the cost of glass, but also due to a tradition in which defence had been a consideration.
Lower in the social scale, improvements in housing standards were general in both rural and urban society. The medieval farmhouse had been ill-lit by small windows (Fig. 6), often unglazed. In the 16th century the ability of those of middling wealth to afford glass, the increasing use of glass rather than oiled linen or wooden shutters for windows, and styles of architecture which embodied larger glazed areas (Figs 7 and 8), brought prosperity to glass makers, and led to the spread of the glass industry over many forested areas of England.
Architectural styles continued to evolve over the 17th and 18th centuries (Louw 1991), with what became the typical ‘Georgian’ sash window requiring numerous panes of glass of increasing size within each casement (Fig. 9). Such windows were commonly inserted into earlier houses (Fig. 10). In high-status buildings, crown glass, with its fine fire-finish, was used for visual effect in the most prominent windows, but broad glass was commonly fitted. Elsewhere in such houses, although its poorer surface finish led to its replacement.
This increase in the use of glass in domestic structures is repeated in industrial buildings throughout the post-medieval period, particularly in the textile mills whose design evolved during the 18th century, in which well-lit workshops required large areas of glass of the cheaper kind, namely broad glass (Figs 11 and 12).